「ギガキャスト」「メガキャスト」のカン違い→アルミ鋳物だから「軽くなる」とは、だれも言っていない
2024年05月26日 08:00
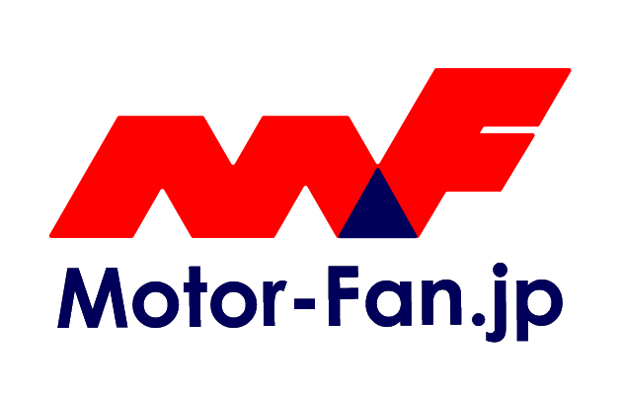
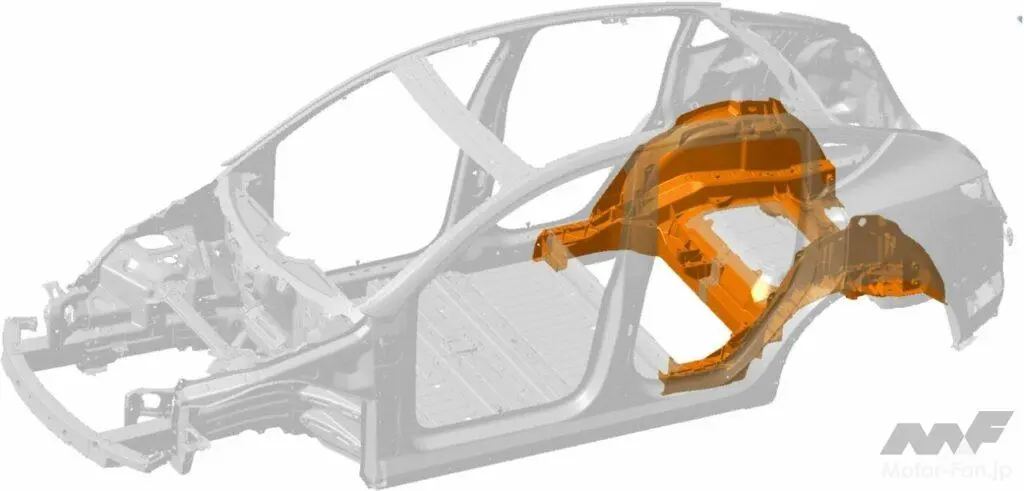
テスラのギガキャスト部品は重たい
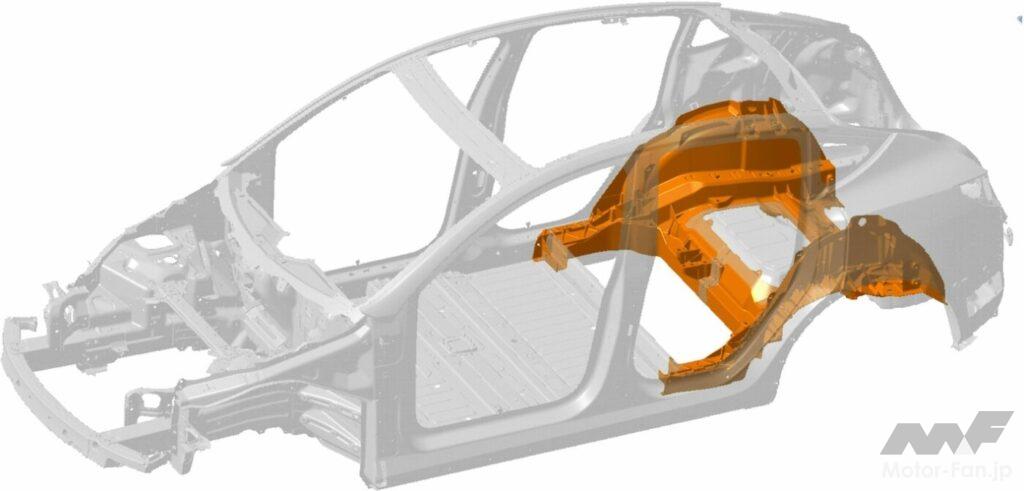
テスラ「モデルY」の左右後輪まわりを一体化したギガキャスト部品【写真01】は、80点以上のプレス成形した薄い鋼板をつなぎ合わせた「モデル3」の構造に代わって部品点数「1」を実現した。【写真02】は左がプレス成形薄板を溶接したテスラ「モデル3」のボディ後ろ側、右はアルミ一体成形の「ギガキャスト」である。
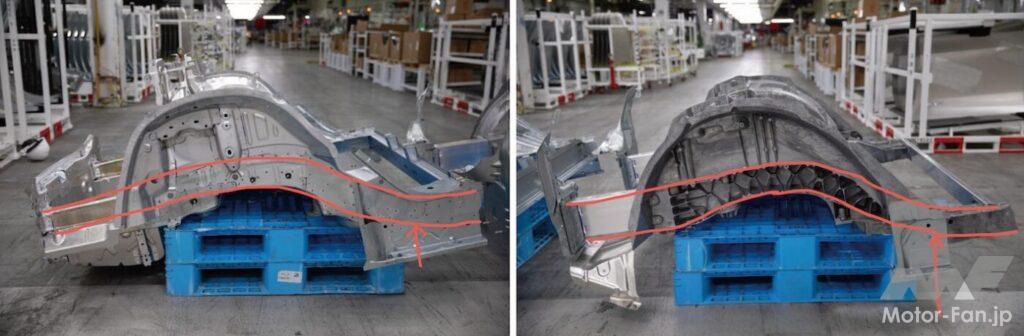
車輪の内側をボディ前後方向に通るサイドメンバー(2本の赤線ではさまれた部分)とその周辺を【写真02】の左側は何枚もの鋼板を重ねてスポット溶接している。もっとも多いところでは4枚重ねになっている。4枚の鋼板を重ねて確実にスポット溶接で留めるのは簡単ではない。重ねる鋼板の厚みや重ねる順序などを吟味しないとうまく留められない。
スポット溶接機の先端は【写真03】のようになっている。親指大のチップで鋼板を両側からはさみ、そこに6000アンペアくらいの大電流を流し、はさんだ部分に電気を流して溶かし、くっつける【写真04】。火花が飛んでいるのは、瞬時に高温になり沸騰した鋼が弾け、重ねた鋼板のスキ間から飛び散るためだ。スポット溶接の要件は、板厚や鋼材の成分、表面の平滑度、チップに加える力(クランプ力)などで変わる。製造ライン上では油汚れの有無なども影響する。
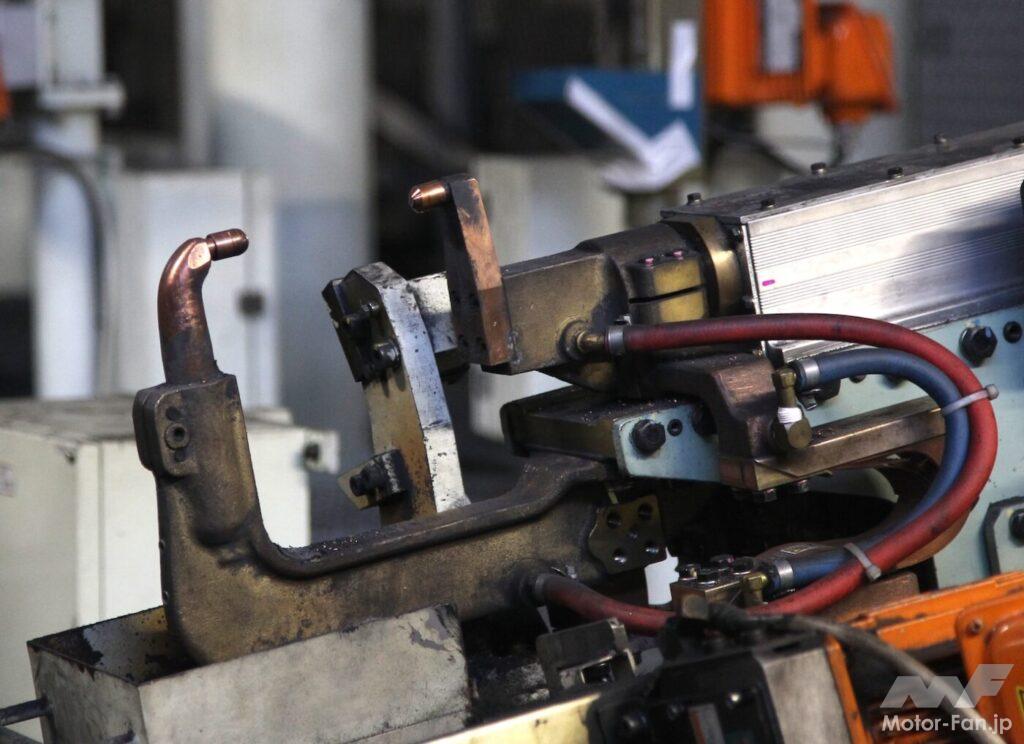
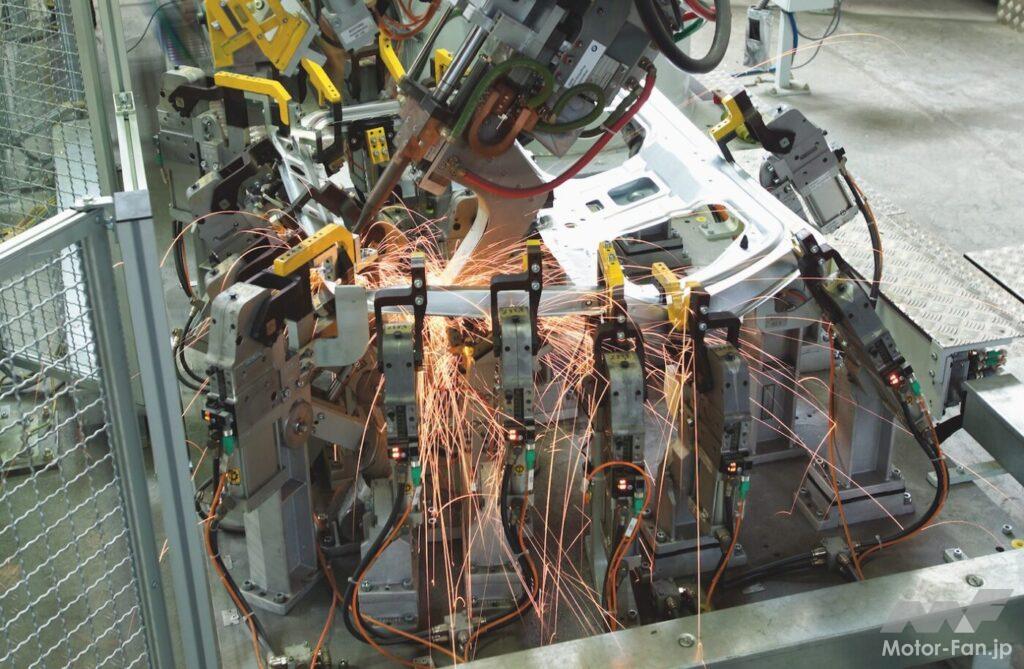
アルミボディでスタートしたテスラにはこうした鋼板溶接のノウハウがなく、溶接しやすい鋼板と溶接方法とをセットで提供してくれるサプライヤーもいなかった。プレス鋼板でモノコック(応力外皮構造)もボディを作るためのサプライチェーンがなかったのだ。
最初の製品であるテスラ「ロードスター」、その次の「モデルS」と、ここから派生した「モデルX」ともにアルミ押出材、アルミ板、アルミ鋳物を組み合わせたボディだった。しかし、低価格化を狙った「モデル3」は一転し骨格を鋼板で作った。
テスラは鋼製モノコックボディの経験があるエンジニアリング会社を買収し、トヨタから格安で譲り受けた元NUMMI(トヨタとGMの車両合弁工場)に鋼製ボディ製造設備を整えた。しかし、量産開始した「モデル3」のボディは接合不良が多かった。その修正のために量産が遅れ、受注のキャンセルが相次いだ。
このころの「モデル3」を購入して分解した技術調査会社を取材すると、一様に「モデル3は薄板4枚重ねの部分のスポット溶接が下手くそ」と聞かされた。クルマ1台をバラバラにする段階で、スポット溶接がうまくくっついていない部分はすぐにわかる。
接合が厄介な鋼板4枚重ね部分をゼロにしたいという動機がギガキャストにつながったのでは、と筆者は想像する。「モデル3」はボディ前端部分がアルミ押出材、ボディ後端部がアルミ鋳物製、ドアやボンネットフードなど「フタもの」がアルミ薄板プレスだったが、衝突エネルギーを吸収する骨格と車室(キャビン)周辺はすべてプレス鋼板製だった。それが「モデルY」では、ボディ後部の左右ホイールアーチ部分が一体型の大きなアルミ鋳物部品になった。
「鋼板溶接が下手くそ」との評は、テスラ自身が接合不良ボディに悩まされたことからも、自覚症状はあったはずだ。そこで量販車「モデルY」では、「モデル3」でとくに苦労した部分を溶接不要の構造にするため、大型鋳造機を扱う伊・IDRA(現在は香港資本・LKエンジニアリングの傘下)から型締め力8500トンという大型鋳造機を購入し、社外の知見も動員して設計したアルミ鋳物製リヤホイールアーチ&リヤフロア一体ユニットを採用した。
これが世の中で「ギガキャスト」と呼ばれる大物鋳物部品である。当然、既存のOEMは注目し、技術評価会社などがこのクルマを購入して分解し、ギガキャスト部分を調査した。筆者は分解と計測を行なった企業を数社取材したが、「モデルY」の「ギガキャスト」部分の重量は約57kgだった。
現在、車両重量1.2トン級の乗用車では、すべての部品とドアなどフタものを取り外したBIW(ボディ・イン・ホワイト)と呼ばれるドンガラの重量は250kg程度である。テスラ「モデルY」は、大きくて重たいバッテリーを取り外せは車両重量1.2トン級である。そのうちの57gkといえば20%以上に当たる。これはかなり重たい。
「ギガキャスト部分を通常のプレス鋼板溶接で作れば、重量は45kg以下になる」「ほぼ同じサイズの乗用車を分解して集めたデータと比較すると、同じ部分が42kgというクルマもある」「テスラのギガキャスト部品は重たい」
これが分解・計測を行なった企業の評価だ。「ギガキャストを採用すればアルミを使って鋼製より軽い部品を作れる」というのは間違いである。むしろ重たくなっている。重たい理由はまず、アルミという素材の特徴だ。アルミの比重は鉄の3分の1だから、同じ強度を得るにはどうしても部材の厚みが増す。つまり、よほど工夫しない限りは軽量化の手段にはならない。
「ギガキャスト」「メガキャスト」にはメリットとデメリットが混在する
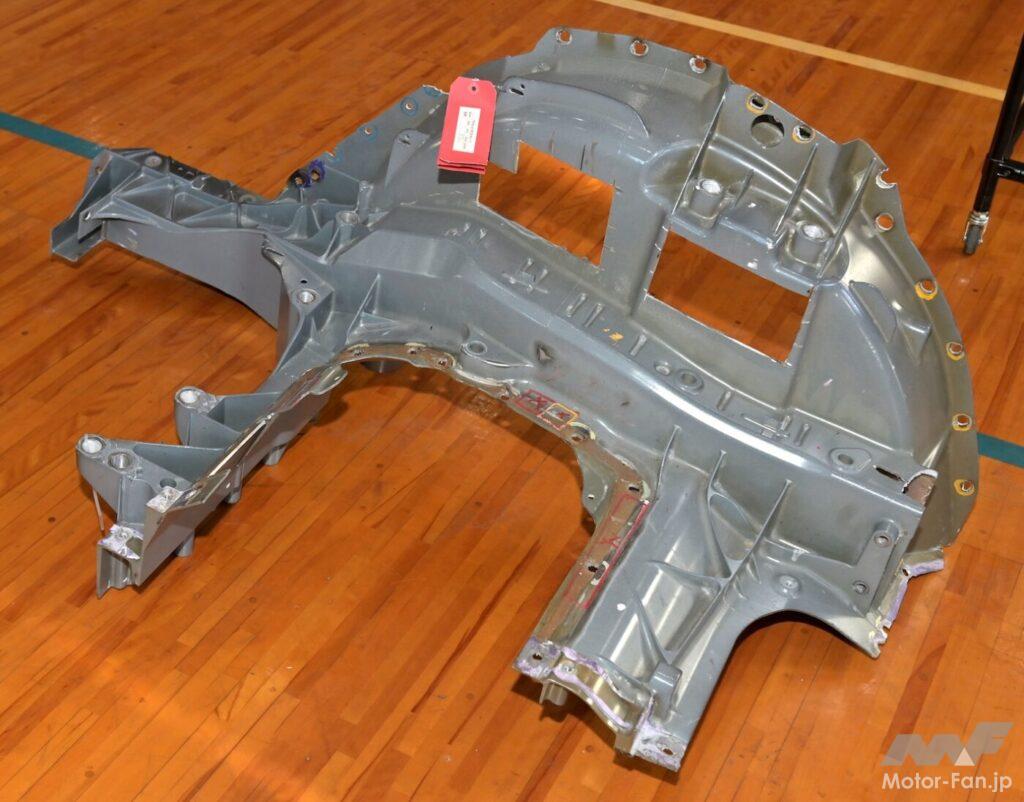
もうひとつの理由は、大型の中号部品の肉厚を薄くすることが難しい点にある。【写真05】は「モデルY」ギガキャスト部品の右側半分でボディ内側から見た様子、【写真06】はそれを反対のホイールハウス側から見た様子だ。四角く穴が空いているのは素材の成分を調べるために切り欠いたためで、実際には塞がっている。【写真07】は左側ホイールハウスの内側に成形されたサイドメンバー部分。実際には左右が一体なった大型の鋳物である。
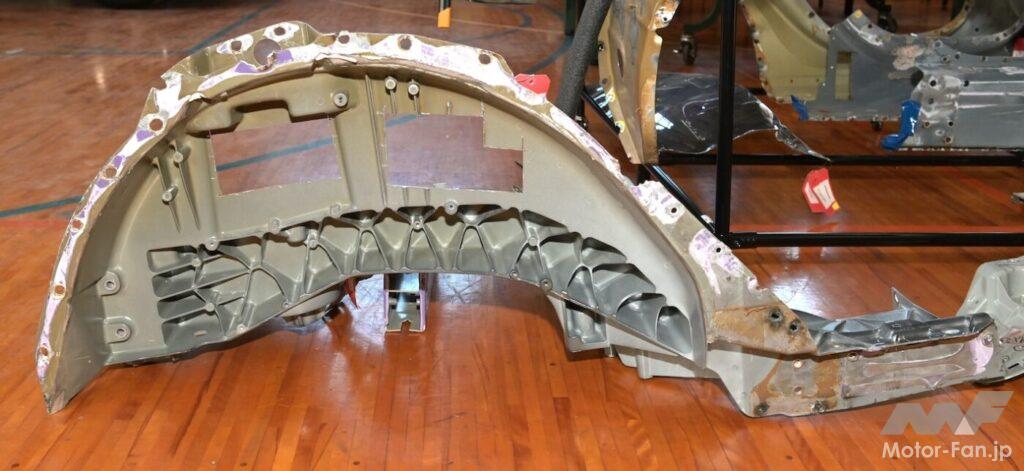
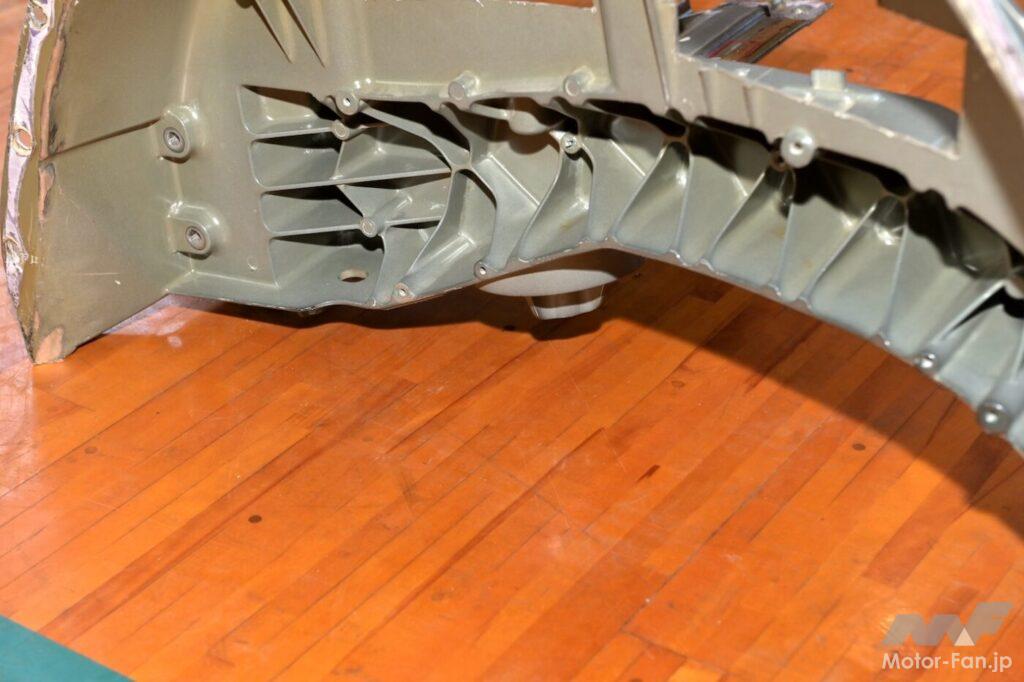
サイドメンバー部分は後部衝突時の衝突エネルギーを吸収し、同時にボディ剛性を確保するため「XXXX」状態に補強リブが成形されている。「X」部分のリブ厚みは3〜4mmある。そのため強度は充分で剛性も高い。ボディ剛性は断面積に比例して高くなるため、むしろ剛性が高すぎる。
補強リブも含めてギガキャスト部品全体をもっと薄くしようとすると、鋳造機の型締め力を高くする必要がある。現在、テスラが使っている型締め力8500トンの鋳造機では、おそらく現在の厚みが限界に近いのではないかと思われる。
肉薄の部分に隅々まで溶けた「アルミ溶湯」を行き渡らせるためには、アルミ溶湯を「押す」圧力と、アルミ溶湯投入口の反対側から「引っ張る」という動作のちょうどいいバランスが求められる。また、高圧でアルミを押し込む場合は、その力に負けないように金型をしっかりと締めておかなければならない。大型鋳造機を使いこなすのは、そう簡単ではない。
しかし、ボディを構成する部品は一体化すると剛性が上がる。ボルト締めや溶接で留めてある部分の「つなぎ目」をなくせば剛性が上がる。その点、ギガキャスト部品はもともと剛性のポテンシャルが高い。ポテンシャルが高いうえに素材の厚みがあるから、なおさら剛性が高い。これは一体鋳造化の大きなメリットだ。
難しいのは寸法精度だ。筆者が実際に見た4例の「ギガキャスト」には、必ず「削って修正した跡」があった。大きな鋳物だから、鋳造する瞬間の微妙な条件の違いによって仕上がり寸法に差が出る。マシンから出てきたギガキャスト部品はその都度修正して使っているようだ。
いまやプレス機でも鋳造機でも、金型の可動部分が動いてマシン側の固定部分と合体するときの微妙なズレ、いわゆる金型と設備とのあいだの「変位量」は、設備設計段階でトポロジー最適化技術による評価が行なわれる。重たい金型が動いて合体するときの微妙な上下傾きや前後左右のズレ(動的クリアランス変化と言う)を抑制している。テスラが使っている8500トン型締め力の鋳造マシンもこの方法で調整されている。
しかし、実際に鋳造を繰り返すなかでは、その日の気温や湿度、素材である「溶けたアルミ」の温度、金型を冷却する水路内の温度分布などの微妙な変化で製品にバラつきが生まれる。ある範囲内の変化であれば、部分的に削るなどして廃棄せずに使う。おそらくテスラは、マシンから出てきたギガキャスト部品の7〜8割を修正して使っているのではないかと思われる。
アルミ鋳造だから軽くなるわけではない。ただし部品点数は確実に減り、剛性は高くなる。寸法精度の追求はなかなか難しい。それと、大型の鋳造マシンはコストが高く、素材であるアルミも鋼板に比べるとコストが高い。「ギガキャスト」「メガキャスト」にはメリットとデメリットが混在するということだ。